How to implement lean management and lean Six Sigma
A lean roadmap helps “lean” practitioners identify and address waste and its drivers, as well as understand how and when to apply the various “lean” approaches in the organization in order to achieve business excellence. A roadmap would also help “lean” practitioners use the full suite of tools to realize the greatest benefits. A “lean” roadmap provides a systematic implementation process: specific actions in order of precedence that are milestones in the journey from mass to “lean” production. A “lean” roadmap is not a cookbook of actions that must be strictly followed for every implementation because every implementation will be singular, in that every company has its own culture, and inheritance policies and systems, which will either support or delay the “lean” journey.
The important point to note is that “lean” should be seen as a direction rather than as a state to be reached after a certain time. The importance of the human factor in lean thinking (LT) cannot be overstated. LT should be viewed as a way of thinking, and both culture and strategy should go in parallel to reach the required results: We need to think, see, and practice “lean”. A “lean” roadmap focuses on leadership, people, “lean” knowledge, objectives, and strategic planning issues, and it provides an organizing framework for enterprise-wide transition. There are also may different road maps or pathway recommended to implement lean. Therefore “lean” needs to be seen as a journey about learning and adding value, not a set of projects and tools.
In order to accomplish benefits of LSS implementation, the creation of a hierarchical infra-structure team is necessary to provide dispersed and specialized training efforts, and to allow for cross-functional project execution. These include full-time Black Belts, who lead improvement projects and typically receive 2-4 weeks of training; Master Black Belts, who receive even more training, and generally serve as instructors and internal consultants; Green Belts, who are part-time improvement specialists that receive less training and perform supporting roles on the improvement projects; and Project Champions who identify strategically important projects for the improvement teams and provide resources and typically receive an orientation to Six Sigma rather than detailed training. However, implementation of LSS in SMEs do not necessarily need a great deal of training and infra-structure team building. For instance, Green Belts are capable of managing LSS projects in the SMEs with the support from project champions.
Having created an infra-strucutre team building, following a road map and methodology has been identified as one of the key top critical success factors of any LSS project. This means unlike lean that was recognised more like a journey, LSS needs structured approach and cook-book with rigid set of methodology and tools to generate the maximum success and avoid failure. However, before deploying the implementation methodology, organisations need to covey readiness phases in which the implementation methodology is embedded in one of the phases.
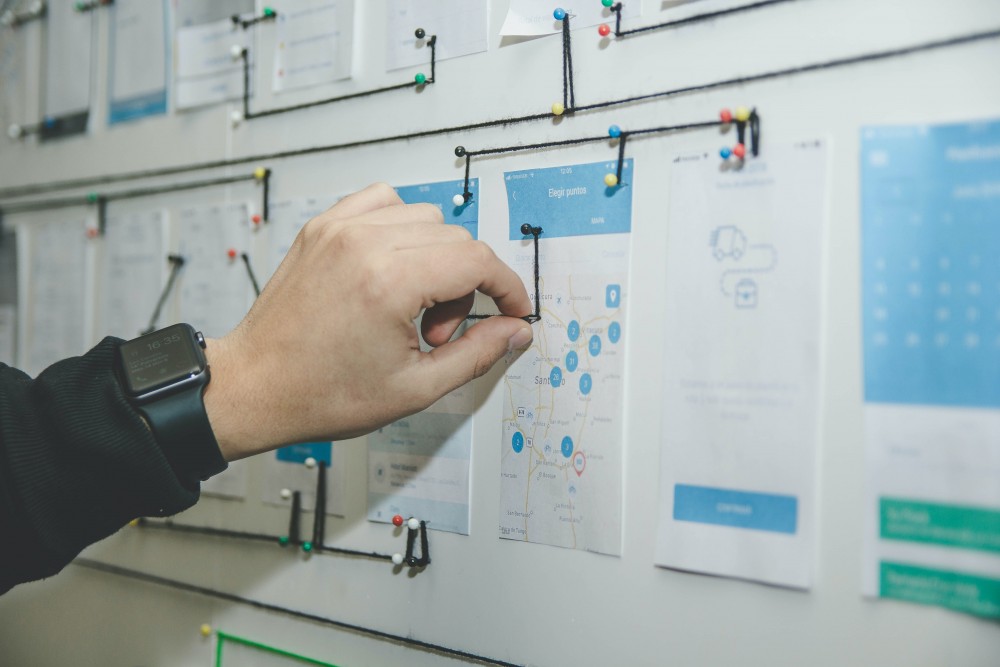