FAQs
In the following section you will find a list of FAQs on Lean Six Sigma
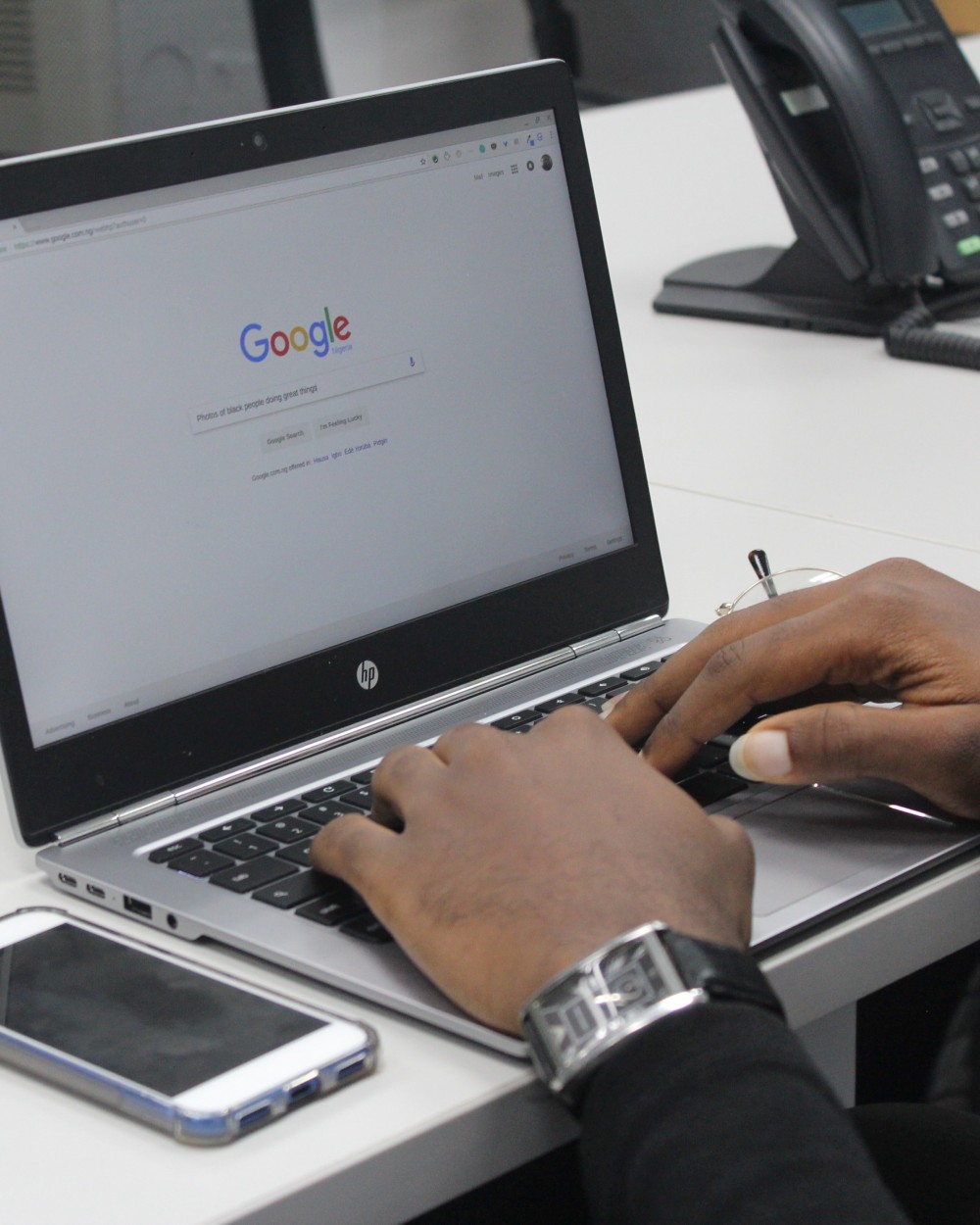
FAQs
Why should I know about lean management?

Efficiency has never been more important to the manufacturing industry than now.
By implementing lean management you can lead on change in your organization to do things differently and work smarter.
Implementing lean manufacturing practices in part means identifying and eliminating the wasteful practices and procedures that are specific to your business, and replacing them with more optimized lean strategies. Lean can improve just-in-time delivery, low wastage, and high-quality products and services for customers. Lean aims at making your organization nimble, agile, and adept at problem-solving and exploiting opportunities
Lean has several benefits for every stakeholder and it can lead to an in-crease in revenue generation, lower costs of production, more efficient and effective business processes and the development of capable and up-skilled teams.
Read more at mk
Why should I know about Lean Six Sigma?

By implementing Lean Six Sigma you can lead on organizational excellence and driving maximizing shareholder value in your organization. Lean Six Sigma will allow your company to achieve success in an increasingly dynamic and complex business environment.
Lean Six Sigma’s continuous improvement angle assures success for the most complex of processes. It has proven to bring a competitive advantage to various businesses such as General Electric, Microsoft, Wipro, and Motorola. Embracing business process improvement will cut down on waste, enhance mind share, and increase the efficiency of your operations. Your business will use its existing resources better. The refinement of business processes will identify talents and parts that require further grooming or distillation to improve the quality of the process.
Read more at SweetProcess
What benefits I and my organization will gain as the result of implementing lean?

Lean management can help you identifying the hidden cost and increasing the efficiency and productivity of your business.
The benefits are manifold:
- Increased product quality: improved efficiency frees up employees and resources for innovation and quality control that would have previously been wasted.
- Improved lead times: as manufacturing processes are streamlined, businesses can better respond to fluctuations in demand and other market variables, resulting in fewer delays and better lead times.
- Sustainability: less waste and better adaptability makes for a business that’s better equipped to thrive well into the future.
- Employee satisfaction: workers know when their daily routine is bloated or packed with unnecessary work, and it negatively affects morale. Lean manufacturing boosts not only productivity, but also employee satisfaction.
- Increased profits: more productivity with less waste and better quality ultimately makes for a more profitable company.
Read more at mk
Is lean management suitable and feasible for SMEs and start-ups?

Yes, lean implementation is associated with continuous improvement philosophy in which small changes can make significant improvements and do not need sophisticated infra-structure, training, knowledge and skills.
Lean management philosophy was first introduced by Toyota. The automotive industry, and more broadly the entire logistics and production management industry was the first to adopt Lean methods and minimize waste. However, the idea then quickly spread to many areas.
No matter how big the company, whether DAX, SME or startup, time wasters and squanders can be eliminated everywhere without reducing the value of the end product.
Lean thinking can be applied to companies and institutions in every conceivable industry. Even hospitals are increasingly trying to streamline processes and eliminate waste.
Read more at tractionwise
What benefits I and my organization will gain as the result of implementing Lean Six Sigma?

Lean Six Sigma is a structured data-driven and systematic approach of solving complicated problems with un-known solutions with the ultimate objective of increased customer satisfaction, profitability, employee empowerment and cost efficiency.
By implementing Lean Six Sigma you can:
- Increase in revenue generation by increasing your capacity to carry out your processes while reducing your worker’s workload per unit in production. Your production will speed up while your quality standards will improve.
- Lower costs of production by cutting down on waste to lower costs while meeting your customers’ expectations. Lean Six Sigma tools will improve problem-solving, infusing your business with a proactive rather than a reactive approach.
- Establish more efficient and effective business processes by optimizing and documenting them. It makes it easy to perform, learn, enhance, and operate for faster growth.
- Develop capable teams as Lean Six Sigma leverages team efforts for improvement. For this reason, it will give your workforce pride in process change and make them more accountable to each other.
Read more at Sweet Process
Is Lean Six Sigma suitable and its implementation feasible for SMEs and start-ups?

Lean Six Sigma is feasible for SMEs. There are many SMEs that have already embarked on Lean Six Sigma phases and even implemented Lean Six sigma projects.
Small businesses face many, if not all, of the challenges of their larger counterparts, but are typically not as well equipped in tackling these challenges.
It is true to say that the traditional textbook approach to Lean Six Sigma deployment has been developed within the big businesses who were amongst the early adopters of this process and performance improvement methodology. However, with judicious application, small businesses can derive almost all of the benefits of Lean Six Sigma with only a fraction of the costs, effort and in much shorter periods of time.
The implementation of Lean Six Sigma is not recommended for start-ups due to its heavily-resource and training orientation.
Read more at Continuous Business Planning
How coaching people can help implementing lean management in SMEs and for start-ups?

Lean management is the journey of doing things differently and needs transformation of people. Employers and managers can play the role of transforming leader and coach people to change before organizational change.
A lean coach creates the conditions for people—whether managers or line workers—to learn and develop the capability to do their work more effectively, at ever-higher quality, and in a way that’s more personally rewarding. By guiding people to view their work—to see—as lean thinkers and take ownership of improvement—to ask why—as lean practitioners, the coach inspires them to do their best work and still strive to do better. Simultaneously, the coach shares lean tools and techniques that their client can use to improve their work process. Through coaching, the learner gains a significant level of autonomy over how to do and improve their work.
Read more at Lean Enterprise Institute